Insights
자동화의 진화, 무인화로 가고 있는 물류
2024.12.12물류현장의 심각해지는 노동력 부족
최근 물류시설을 운영하는 지인들의 공통적인 하소연은 “현장에 일할 사람을 구하기 어렵다”라는 것이다. 이전에도 이런 얘기들은 있었다. 하지만 들여다보면 이전의 그것과는 사뭇 다르다. 인력수급시장에 노동력은 있음에도 힘든 물류현장을 회피하던 차원과는 달리 지금은 구조적으로 노동력이 부족해지고 있다는 점에서 그 심각성이 있다. 출산율의 저하로 인한 인구의 급격한 감소로 국가소멸까지 거론되는 대한민국의 인구사회학적 문제는 본 기고의 주제인 물류 분야에서마저 큰 변혁을 불러일으킬 것이다. 필자는 사회학자는 아니다. 오랜 기간 물류효율화를 과제로 물류컨설팅 및 시스템설계를 해 온 물류 분야의 전문가이다. 그러한 관점에서 바라본 물류자동화가 과거 흘러왔던 것을 겪어온 경험을 기반으로 앞으로 어떤 방향으로 전개될 것인가에 대해 생각을 풀어보고자 한다.
물류자동화의 레벨은 그림1과 같이 다섯 단계로 나눠볼 수 있다. 미래 물류의 전개 방향을 제시하는 부분은 레벨5인데, AI 기술을 기반으로 지능화, 무인화된 물류센터가 점차 늘어날 것이다. 다만 새로운 레벨이 이전의 레벨을 아주 소멸시키지는 않을 것이며, 마지막 단계의 레벨은 예상보다 빠른 시기에 현실화될 것이다. 즉, Stacker Crane Type의 자동창고(AS/RS)처럼 레벨3에 위치하는 설비가 레벨4, 레벨5 설비의 확산으로 인해 도태될 것인가에 대해 묻는다면 (일정 수요가 줄어들기는 해도) 결코 사라지지는 않을 것이라고 답한다. 그 이유로는 시장규모, 수출입물량의 확대, 최소생산량의 규모 등 사업과 현장의 특성에 따라 낮은 레벨에 위치하는 설비가 적정하고 효율적일 수 있기 때문이다. 예를 들어 대량생산시대의 상징인 레벨2의 컨베이어가 지금도 여전히 많은 도입이 이뤄지고 있고 앞으로도 완전히 이송용 AMR로 전량 대체되지는 않을 것으로 전망하는 이유 역시 그 효율성과 처리 Capacity 측면에서 찾을 수 있다. 존재 또는 소멸이라는 이분법이 아니고 일정 부분의 공존을 유지할 것이다. 그러나 시장에서의 사용자(고객)의 요구가 매우 빠른 속도의 다품종 소량화에 있는 한, 이에 부응할 수 있도록 레벨5의 지능화, 무인화로 갈 것이라는 것은 거스를 수 없는 대세가 될 것이다. 그 이유를 설명해 보자. 무엇보다 노동력의 부족을 들지 않을 수 없다. 자동화는 사람과 기계의 조합이므로 자동화설비를 운영해야 할 사람이 필요하다. 많은 사례에서 물류 자동화설비를 도입했음에도 유의미할 정도로 사람이 줄어들지 않은 경우를 보아왔다. 오히려 사람이 더 늘어난 경우마저 있다. 그런데 앞으로 이러한 것은 더 이상 용인되지 않을 것이다. 물류설비를 운용할 사람이 없기 때문에 사람을 쓰지 않고 돌아가는 물류설비가 필요해진다. 과거에도 무인화에 대한 기업들의 수요는 존재했지만 기술적인 한계로 실현에 어려움을 겪었다. 그러나 현재는 필연적인 인구감소 문제와, 이러한 긴급한 요청에 부응하는 AI·로봇 기술의 발전으로 진정한 의미의 무인화 물류설비가 등장하게 되었다. 지금도 물류현장에서는 양질의 노동력 부족으로 시달리고 있는데 급격하게 인구가 줄어드는 다가올 미래를 적절한 대비 없이 맞는다면 어떨 것인가를 생각하면 매우 걱정스러운 일이다. 수요업체와 공급업체 모두 각별한 선행적 준비가 필요하다.
무인화 물류설비의 대표주자: 물류로봇
물류센터를 구성하는 주요 공정은 입하-하차-입하대기-입하검수-(팔레트 적재)-입고/적치-보관-(팔레트 해체)-보충입출고-출고/피킹-분류-출고검수-포장-(팔레트 적재)-출하검수-출하대기-상차-출하, 그리고 공정 간 이동 등으로 이뤄진다. 여기서 잠깐 로봇의 정의를 살펴보자. 사전적으로 로봇이란 ‘어떤 작업이나 동작을 자동으로 하는 기계장치’로 설명한다. 이 정의대로라면 물류자동화 설비 중 로봇이 아닌 게 없는 셈이 된다. 전술한 바와 같이 자동화설비는 사람에 의해 운영되므로 본 기고문에서는 이와 차별적으로 사람을 쓰지 않는 물류설비라는 의미로 무인화 물류설비라는 용어를 제시하였고 이에 해당하는 것들을 물류로봇이라고 별도 분류하고 있다. 아직은 기술의 성숙도, 적용 조건의 제한성, 처리 속도 및 Capacity, 실적용 사례의 정도, 경제성 등의 극복해야 할 과제를 일부 안고 있지만 화물차에 물건을 올리고 내리는 상하차로봇(Devanning robot), 팔레트에 크기와 모양이 다양한 상품(Mixed SKU)을 쌓거나 해체하는 Mixed 팔레타이징로봇(Palletizing robot), 상품을 이송하는 AMR, 낱개 상품을 하나씩 골라내는 피킹로봇(Picking robot), 상품을 배송지별로 분류하는 분류로봇(Sorting robot), 완전재단형 자동포장기, 팔레트를 들고 나르는 무인지게차 등이 이에 해당한다.
지금 우리는 왜 이러한 물류로봇에 주목해야 하는 것일까? 그것은 당연히 큰 장점을 갖고 있기 때문이다. 첫째는 심각한 구인난의 유일한 돌파구이자 해결책이라는 점이다. 물류로봇은 드라마틱한 인력 절감 효과가 있다. 또한 24/7, 즉 24시간, 7일 내내 일을 해낼 수 있기 때문에 같은 물류시설에서 처리해내는 물동량의 Throughput이 많아지고 Leadtime이 짧아진다. 이러한 물류생산성 증가는 기업경쟁력 제고로 이어질 수 있다.
둘째는 작업 결과의 균질성이다. 사람은 경험과 숙련도에 따라 생산성 차이가 나고 작업의 질 측면에서도 차이가 나는데 물류로봇은 작업 물동량이 주어지는 한 모두 주어진 사양과 Capacity에서 열심히 일한다.
셋째는 안전사고의 발생빈도가 줄어든다는 것이다. 무거운 물건을 다루는 일이나 고강도 반복 작업을 물류로봇이 대신하니 안전사고는 줄기 마련이다. 로봇은 정해진 일을 정확하게 수행하기 때문에 돌발상황이 줄어들고 작업환경도 정돈된다. 물류로봇의 중요한 설계포인트 중 하나가 안전(Safety)이기도 하다.
무의미한 ROI 분석
대규모 물류시설 투자계획 컨설팅 수행 시 반드시 해야 하는 과제 중 하나로 ROI 분석이 있다. 그런데 최근 수행한 한 프로젝트에서는 매우 큰 금액의 투자를 필요로 했지만 이 과제를 수행하지 않았다. (내부적으로는 투자심의 또는 이에 준하는 절차가 있겠지만). 이 고객사 또한 대부분 물류센터에서 안고 있는 애로사항과 같이 운영하는 기존 2개의 물류센터에서 인력 부족 및 구인난을 겪어오고 있다. 그래서 얼마를 투자해서 얼마 만에 회수하고 식의 ROI 분석에 큰 의미를 두지 않았다. 초기투자비가 더 들더라도 적은 인력으로도 운영이 가능하게 하는 것이 본 사례에서의 고객의 요구사항이었다. 필자의 주장과 일맥상통하는 사례에 해당한다. 초기 투자비(CAPEX)보다 운영비(OPEX)를 중시해야 하는 시대이다. 앞으로는 더더욱 그러할 것이다. 이를 구현하는 수단이 바로 물류로봇이다. 본 사례에서는 ‘실사례를 통해 검증될 수 있을 것’이라는 고객사 요구조건이 있었고, 이 요구조건을 충족한 자동포장라인, 팔레트 이송용 AMR 등 무인화설비 또는 인력소요를 최소화하는 고도 자동화설비를 제안하여 대부분 반영되었다. 물류로봇을 채택하는 데 경제성 측면에서도 우호적인 환경이 조성되고 있다. 인건비(Labor Cost)는 점증하고 로봇 가격(Robot Price)은 갈수록 낮아져 이미 1980년대에 크로스가 발생하여 해를 거듭할수록 그 격차가 벌어지고 있다는 흥미로운 통계가 있다. 이는 기존의 산업용로봇은 물론 머지않아 물류로봇에 있어서도 적용되게 될 것으로 보인다. 이처럼 명확한 효과성 또한 물류로봇을 도입하는 데 ROI를 분석하지 않아도 되는 요인으로 작용할 듯하다.
상용화로 가고 있는 물류로봇
물류의 DX(Digital Transformation)를 통한 스마트물류 구현의 3가지 키워드는 지능화, 초연결성, 기술의 융·복합화를 거론한다. 이의 적용을 적절히 잘하면 스마트물류가 되는 것이다. 정부의 스마트물류센터 인증에서도 이러한 관점에서 평가가 이뤄진다. 물류설비에서 지능화란 인공지능(AI) 기술의 반영인데 요소기술로는 CVT(Computer Vision Technologies)와 머신러닝 (ML)기술이 핵심을 이룬다. 그런데 적어도 사람만큼의 정확성과 퍼포먼스를 내기 위해서는 극복해야 할 제약조건들이 많다. 물류센터 현장에서 발생하는 다양한 경우와 상황을 로봇에게 모두 학습시킨다는 것이 매우 어려운 일이기 때문이다. 그럼에도 불구하고 제약조건과 기술적 성숙도의 한계를 극복하고 유의미한 Spec & Capacity, 경제성을 갖는 물류로봇들이 머지않은 미래에 속속 상용화 출시될 것으로 믿고 있다. 그 이유는 해당 요소기술과 응용기술의 발전이 비약적으로 진행됨과 동시에 이 분야에 세계적으로 많은 스타트업 기업들의 탄생이 지속되고 있고 많은 돈이 몰리고 있다는 점이다. 노동력의 부족은 비단 우리나라만의 문제가 아니라 세계적인 추세에 접어들었다는 예측이 지배적이기 때문에 더더욱 글로벌 공급업체들은 이를 노려 무인화설비의 개발/보급에 많은 투자를 하는 것이다. 성공 사례들의 등장은 더 많은 관련 기업들의 참여를 불러일으키는 선순환의 고리를 만들게 된다. 더불어 PoC 프로젝트 및 실적용 사례의 등장이 이어지고 있다는 것 또한 고무적이다. 전술한 공정별 물류로봇들 중에서 이미 상용화의 빠른 진전이 이뤄진 것은 주로 많은 인력이 투입되고 있었던 (또는 있는) 공정이다. 어느 물류센터의 현장을 가봐도 공통적으로 많은 인력이 몰려 있는 공정은 피킹/분류, 포장 작업이다. 관련 논문에 자주 인용되는 수치 중 물류센터 내 전래적 낱개 취급 사용 공수 실적내역 (Warehouse Split Case Labor Hours by Job Functions)을 보면 피킹 유관작업(Order Selection) 및 보충(Replenishment) 작업에 각각 53.1%와 21.4%, 포장(Packing)에 7.6%가 소요된다는 것으로 설명할 수 있다. (단, 이 비율은 절대적인 것은 아니고 물류현장에 따라 차이가 난다. 필자가 수행한 한 프로젝트의 포장 작업자 구성비는 25%에 달한다). 다시 말해 피킹의 유관 작업에 활용되는 설비들, 로봇이 피킹할 상품을 작업자에게 가져다주는 AMR 기반의 GTP 시스템(Goods-to-Person), AMR 기반의 셔틀 시스템, 큐브형 스토리지(Cubic Storage) 등이 큰 성공을 거둘 수 있었던 환경적 기반이 되었던 셈이다. 다만 Pick & Put 동작에 있어서는 현장의 여러 가지 실운영 조건 중 혼적 상태에서 밑에 감춰져 보이지 않는 상품의 피킹, 한 번에 다양한 복수 상품의 피킹 등 로봇이 인간의 판단력과 작업생산성에는 미치지 못함으로써 지금까지는 실적용이 기대만큼 확산되지 못하고 있다. 그러나 관련기업들이 확보해 가고 있는 References들을 보면 머지않은 미래에 많은 현장에서 Pick & Put 동작도 사람 대신 로봇으로 대체될 수 있을 것으로 예상된다. GTP라는 용어에서 파생되어 로봇이 로봇에게 피킹할 상품을 가져다주는 GTR(Goods-to-Robot)이라는 용어가 익숙해질 날이 머지않은 듯하다. 포장 작업 역시 많은 인력에 의존해 왔던 공정인데 세계적으로 다수의 기업이 고객의 주문량의 체적에 맞춘 재단형 무인화 포장장비를 상용화 출시하고 있다. 전후 공정/구간 이동용 AMR의 상용화 및 적용은 확산되고 있고 이외에도 Mixed 팔레타이징로봇, 상하차로봇 등도 활발한 PoC 및 실적용 사례가 나타나고 있는 등 물류센터 공정 운영 전체에 걸쳐 사람 대신 물류로봇으로 대체되는 무인 물류센터의 등장이 공상과학 속 이야기가 아닐 수도 있다.
글 | 두산로지스틱스솔루션 한종수 총괄위원 / 아주대학교 공학대학원 겸임교수
최근 물류시설을 운영하는 지인들의 공통적인 하소연은 “현장에 일할 사람을 구하기 어렵다”라는 것이다. 이전에도 이런 얘기들은 있었다. 하지만 들여다보면 이전의 그것과는 사뭇 다르다. 인력수급시장에 노동력은 있음에도 힘든 물류현장을 회피하던 차원과는 달리 지금은 구조적으로 노동력이 부족해지고 있다는 점에서 그 심각성이 있다. 출산율의 저하로 인한 인구의 급격한 감소로 국가소멸까지 거론되는 대한민국의 인구사회학적 문제는 본 기고의 주제인 물류 분야에서마저 큰 변혁을 불러일으킬 것이다. 필자는 사회학자는 아니다. 오랜 기간 물류효율화를 과제로 물류컨설팅 및 시스템설계를 해 온 물류 분야의 전문가이다. 그러한 관점에서 바라본 물류자동화가 과거 흘러왔던 것을 겪어온 경험을 기반으로 앞으로 어떤 방향으로 전개될 것인가에 대해 생각을 풀어보고자 한다.
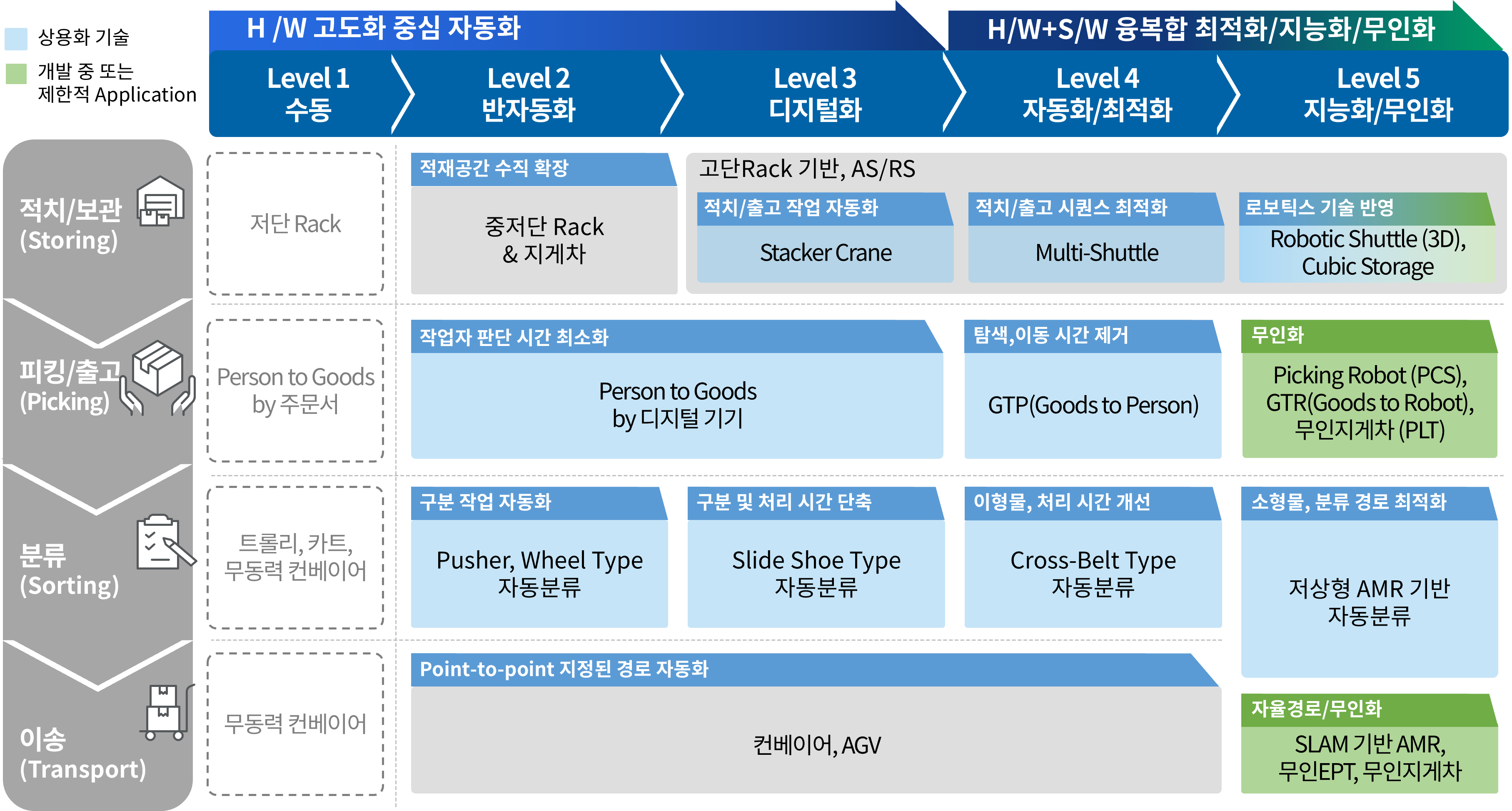
▲(그림1) 물류자동화 레벨
물류자동화의 레벨은 그림1과 같이 다섯 단계로 나눠볼 수 있다. 미래 물류의 전개 방향을 제시하는 부분은 레벨5인데, AI 기술을 기반으로 지능화, 무인화된 물류센터가 점차 늘어날 것이다. 다만 새로운 레벨이 이전의 레벨을 아주 소멸시키지는 않을 것이며, 마지막 단계의 레벨은 예상보다 빠른 시기에 현실화될 것이다. 즉, Stacker Crane Type의 자동창고(AS/RS)처럼 레벨3에 위치하는 설비가 레벨4, 레벨5 설비의 확산으로 인해 도태될 것인가에 대해 묻는다면 (일정 수요가 줄어들기는 해도) 결코 사라지지는 않을 것이라고 답한다. 그 이유로는 시장규모, 수출입물량의 확대, 최소생산량의 규모 등 사업과 현장의 특성에 따라 낮은 레벨에 위치하는 설비가 적정하고 효율적일 수 있기 때문이다. 예를 들어 대량생산시대의 상징인 레벨2의 컨베이어가 지금도 여전히 많은 도입이 이뤄지고 있고 앞으로도 완전히 이송용 AMR로 전량 대체되지는 않을 것으로 전망하는 이유 역시 그 효율성과 처리 Capacity 측면에서 찾을 수 있다. 존재 또는 소멸이라는 이분법이 아니고 일정 부분의 공존을 유지할 것이다. 그러나 시장에서의 사용자(고객)의 요구가 매우 빠른 속도의 다품종 소량화에 있는 한, 이에 부응할 수 있도록 레벨5의 지능화, 무인화로 갈 것이라는 것은 거스를 수 없는 대세가 될 것이다. 그 이유를 설명해 보자. 무엇보다 노동력의 부족을 들지 않을 수 없다. 자동화는 사람과 기계의 조합이므로 자동화설비를 운영해야 할 사람이 필요하다. 많은 사례에서 물류 자동화설비를 도입했음에도 유의미할 정도로 사람이 줄어들지 않은 경우를 보아왔다. 오히려 사람이 더 늘어난 경우마저 있다. 그런데 앞으로 이러한 것은 더 이상 용인되지 않을 것이다. 물류설비를 운용할 사람이 없기 때문에 사람을 쓰지 않고 돌아가는 물류설비가 필요해진다. 과거에도 무인화에 대한 기업들의 수요는 존재했지만 기술적인 한계로 실현에 어려움을 겪었다. 그러나 현재는 필연적인 인구감소 문제와, 이러한 긴급한 요청에 부응하는 AI·로봇 기술의 발전으로 진정한 의미의 무인화 물류설비가 등장하게 되었다. 지금도 물류현장에서는 양질의 노동력 부족으로 시달리고 있는데 급격하게 인구가 줄어드는 다가올 미래를 적절한 대비 없이 맞는다면 어떨 것인가를 생각하면 매우 걱정스러운 일이다. 수요업체와 공급업체 모두 각별한 선행적 준비가 필요하다.
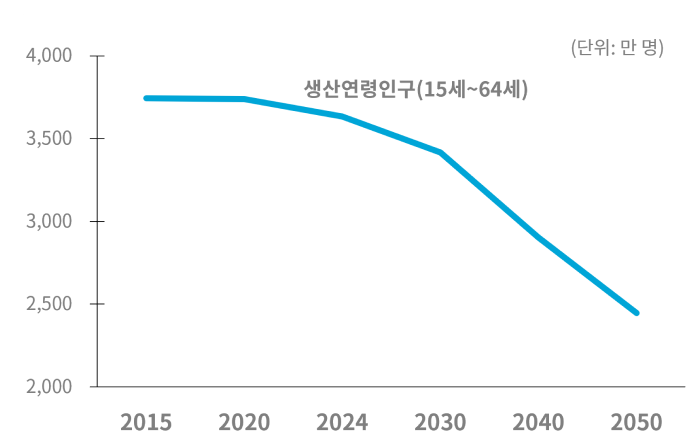
▲(그림2) 우리나라의 생산가능인구 추이 (만 명, 통계청)
무인화 물류설비의 대표주자: 물류로봇
물류센터를 구성하는 주요 공정은 입하-하차-입하대기-입하검수-(팔레트 적재)-입고/적치-보관-(팔레트 해체)-보충입출고-출고/피킹-분류-출고검수-포장-(팔레트 적재)-출하검수-출하대기-상차-출하, 그리고 공정 간 이동 등으로 이뤄진다. 여기서 잠깐 로봇의 정의를 살펴보자. 사전적으로 로봇이란 ‘어떤 작업이나 동작을 자동으로 하는 기계장치’로 설명한다. 이 정의대로라면 물류자동화 설비 중 로봇이 아닌 게 없는 셈이 된다. 전술한 바와 같이 자동화설비는 사람에 의해 운영되므로 본 기고문에서는 이와 차별적으로 사람을 쓰지 않는 물류설비라는 의미로 무인화 물류설비라는 용어를 제시하였고 이에 해당하는 것들을 물류로봇이라고 별도 분류하고 있다. 아직은 기술의 성숙도, 적용 조건의 제한성, 처리 속도 및 Capacity, 실적용 사례의 정도, 경제성 등의 극복해야 할 과제를 일부 안고 있지만 화물차에 물건을 올리고 내리는 상하차로봇(Devanning robot), 팔레트에 크기와 모양이 다양한 상품(Mixed SKU)을 쌓거나 해체하는 Mixed 팔레타이징로봇(Palletizing robot), 상품을 이송하는 AMR, 낱개 상품을 하나씩 골라내는 피킹로봇(Picking robot), 상품을 배송지별로 분류하는 분류로봇(Sorting robot), 완전재단형 자동포장기, 팔레트를 들고 나르는 무인지게차 등이 이에 해당한다.
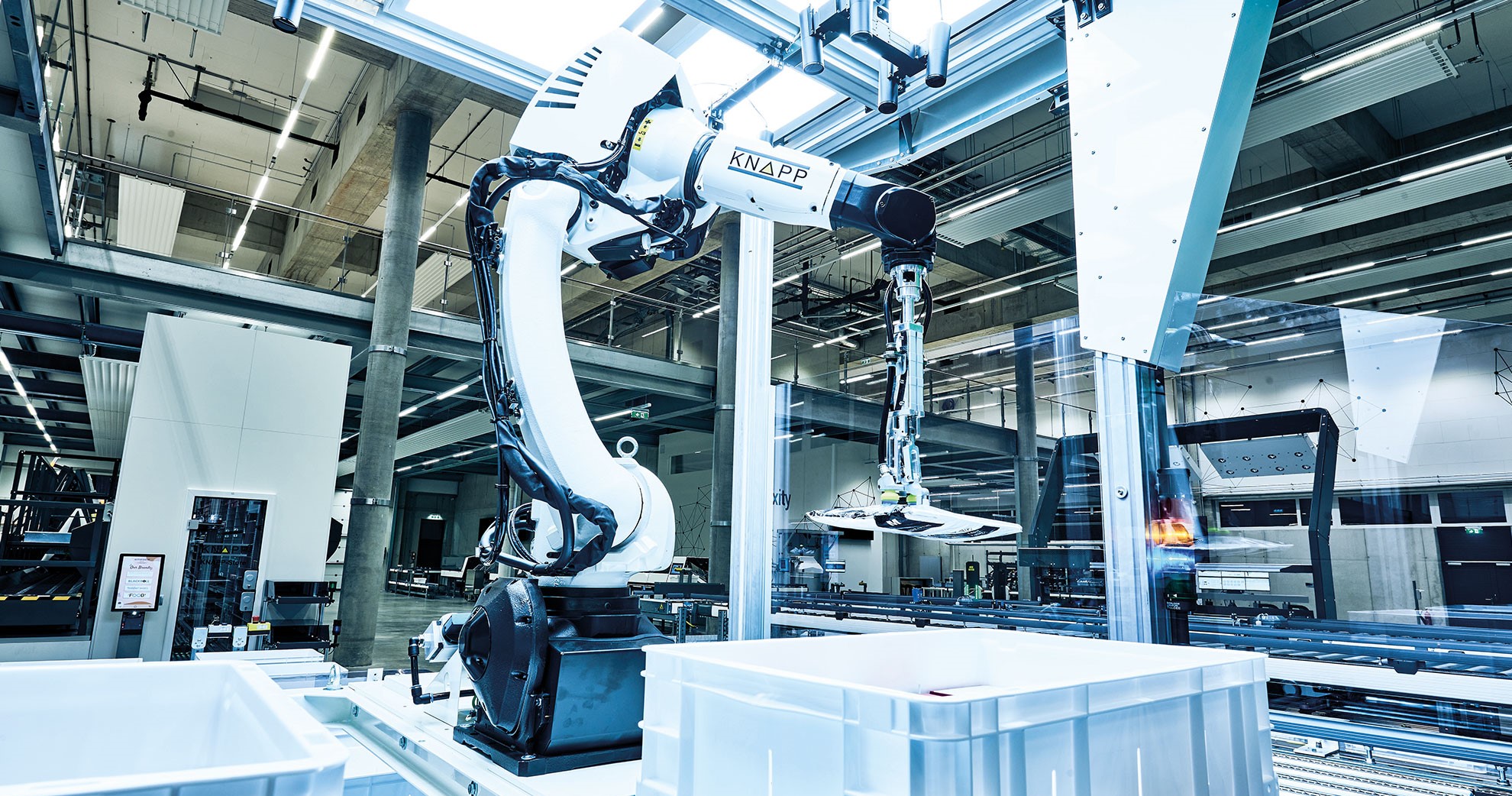
▲(그림3) 피킹로봇
지금 우리는 왜 이러한 물류로봇에 주목해야 하는 것일까? 그것은 당연히 큰 장점을 갖고 있기 때문이다. 첫째는 심각한 구인난의 유일한 돌파구이자 해결책이라는 점이다. 물류로봇은 드라마틱한 인력 절감 효과가 있다. 또한 24/7, 즉 24시간, 7일 내내 일을 해낼 수 있기 때문에 같은 물류시설에서 처리해내는 물동량의 Throughput이 많아지고 Leadtime이 짧아진다. 이러한 물류생산성 증가는 기업경쟁력 제고로 이어질 수 있다.
둘째는 작업 결과의 균질성이다. 사람은 경험과 숙련도에 따라 생산성 차이가 나고 작업의 질 측면에서도 차이가 나는데 물류로봇은 작업 물동량이 주어지는 한 모두 주어진 사양과 Capacity에서 열심히 일한다.
셋째는 안전사고의 발생빈도가 줄어든다는 것이다. 무거운 물건을 다루는 일이나 고강도 반복 작업을 물류로봇이 대신하니 안전사고는 줄기 마련이다. 로봇은 정해진 일을 정확하게 수행하기 때문에 돌발상황이 줄어들고 작업환경도 정돈된다. 물류로봇의 중요한 설계포인트 중 하나가 안전(Safety)이기도 하다.
무의미한 ROI 분석
대규모 물류시설 투자계획 컨설팅 수행 시 반드시 해야 하는 과제 중 하나로 ROI 분석이 있다. 그런데 최근 수행한 한 프로젝트에서는 매우 큰 금액의 투자를 필요로 했지만 이 과제를 수행하지 않았다. (내부적으로는 투자심의 또는 이에 준하는 절차가 있겠지만). 이 고객사 또한 대부분 물류센터에서 안고 있는 애로사항과 같이 운영하는 기존 2개의 물류센터에서 인력 부족 및 구인난을 겪어오고 있다. 그래서 얼마를 투자해서 얼마 만에 회수하고 식의 ROI 분석에 큰 의미를 두지 않았다. 초기투자비가 더 들더라도 적은 인력으로도 운영이 가능하게 하는 것이 본 사례에서의 고객의 요구사항이었다. 필자의 주장과 일맥상통하는 사례에 해당한다. 초기 투자비(CAPEX)보다 운영비(OPEX)를 중시해야 하는 시대이다. 앞으로는 더더욱 그러할 것이다. 이를 구현하는 수단이 바로 물류로봇이다. 본 사례에서는 ‘실사례를 통해 검증될 수 있을 것’이라는 고객사 요구조건이 있었고, 이 요구조건을 충족한 자동포장라인, 팔레트 이송용 AMR 등 무인화설비 또는 인력소요를 최소화하는 고도 자동화설비를 제안하여 대부분 반영되었다. 물류로봇을 채택하는 데 경제성 측면에서도 우호적인 환경이 조성되고 있다. 인건비(Labor Cost)는 점증하고 로봇 가격(Robot Price)은 갈수록 낮아져 이미 1980년대에 크로스가 발생하여 해를 거듭할수록 그 격차가 벌어지고 있다는 흥미로운 통계가 있다. 이는 기존의 산업용로봇은 물론 머지않아 물류로봇에 있어서도 적용되게 될 것으로 보인다. 이처럼 명확한 효과성 또한 물류로봇을 도입하는 데 ROI를 분석하지 않아도 되는 요인으로 작용할 듯하다.
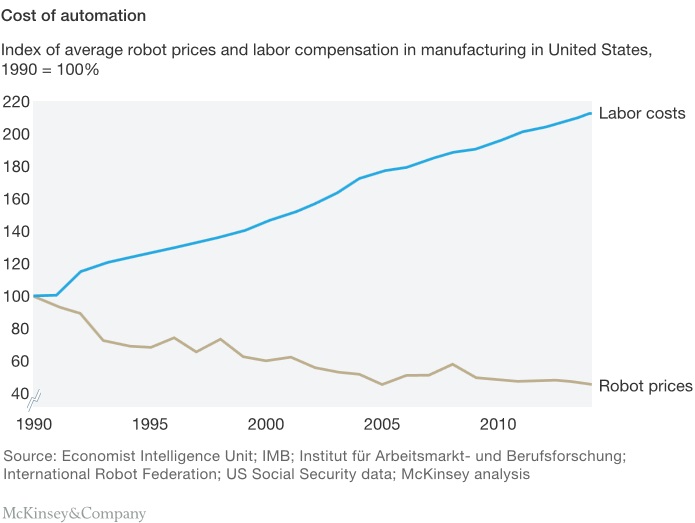
▲(그림4) Robot Price vs Labor Cost (McKinsey & Company, 2017)
The cost of which is $8 an hour, whereas it is $15 an hour for a
human worker, according to a recent article on wired.
Many companies are even replacing human labor with automation-2022
The cost of which is $8 an hour, whereas it is $15 an hour for a
human worker, according to a recent article on wired.
Many companies are even replacing human labor with automation-2022
상용화로 가고 있는 물류로봇
물류의 DX(Digital Transformation)를 통한 스마트물류 구현의 3가지 키워드는 지능화, 초연결성, 기술의 융·복합화를 거론한다. 이의 적용을 적절히 잘하면 스마트물류가 되는 것이다. 정부의 스마트물류센터 인증에서도 이러한 관점에서 평가가 이뤄진다. 물류설비에서 지능화란 인공지능(AI) 기술의 반영인데 요소기술로는 CVT(Computer Vision Technologies)와 머신러닝 (ML)기술이 핵심을 이룬다. 그런데 적어도 사람만큼의 정확성과 퍼포먼스를 내기 위해서는 극복해야 할 제약조건들이 많다. 물류센터 현장에서 발생하는 다양한 경우와 상황을 로봇에게 모두 학습시킨다는 것이 매우 어려운 일이기 때문이다. 그럼에도 불구하고 제약조건과 기술적 성숙도의 한계를 극복하고 유의미한 Spec & Capacity, 경제성을 갖는 물류로봇들이 머지않은 미래에 속속 상용화 출시될 것으로 믿고 있다. 그 이유는 해당 요소기술과 응용기술의 발전이 비약적으로 진행됨과 동시에 이 분야에 세계적으로 많은 스타트업 기업들의 탄생이 지속되고 있고 많은 돈이 몰리고 있다는 점이다. 노동력의 부족은 비단 우리나라만의 문제가 아니라 세계적인 추세에 접어들었다는 예측이 지배적이기 때문에 더더욱 글로벌 공급업체들은 이를 노려 무인화설비의 개발/보급에 많은 투자를 하는 것이다. 성공 사례들의 등장은 더 많은 관련 기업들의 참여를 불러일으키는 선순환의 고리를 만들게 된다. 더불어 PoC 프로젝트 및 실적용 사례의 등장이 이어지고 있다는 것 또한 고무적이다. 전술한 공정별 물류로봇들 중에서 이미 상용화의 빠른 진전이 이뤄진 것은 주로 많은 인력이 투입되고 있었던 (또는 있는) 공정이다. 어느 물류센터의 현장을 가봐도 공통적으로 많은 인력이 몰려 있는 공정은 피킹/분류, 포장 작업이다. 관련 논문에 자주 인용되는 수치 중 물류센터 내 전래적 낱개 취급 사용 공수 실적내역 (Warehouse Split Case Labor Hours by Job Functions)을 보면 피킹 유관작업(Order Selection) 및 보충(Replenishment) 작업에 각각 53.1%와 21.4%, 포장(Packing)에 7.6%가 소요된다는 것으로 설명할 수 있다. (단, 이 비율은 절대적인 것은 아니고 물류현장에 따라 차이가 난다. 필자가 수행한 한 프로젝트의 포장 작업자 구성비는 25%에 달한다). 다시 말해 피킹의 유관 작업에 활용되는 설비들, 로봇이 피킹할 상품을 작업자에게 가져다주는 AMR 기반의 GTP 시스템(Goods-to-Person), AMR 기반의 셔틀 시스템, 큐브형 스토리지(Cubic Storage) 등이 큰 성공을 거둘 수 있었던 환경적 기반이 되었던 셈이다. 다만 Pick & Put 동작에 있어서는 현장의 여러 가지 실운영 조건 중 혼적 상태에서 밑에 감춰져 보이지 않는 상품의 피킹, 한 번에 다양한 복수 상품의 피킹 등 로봇이 인간의 판단력과 작업생산성에는 미치지 못함으로써 지금까지는 실적용이 기대만큼 확산되지 못하고 있다. 그러나 관련기업들이 확보해 가고 있는 References들을 보면 머지않은 미래에 많은 현장에서 Pick & Put 동작도 사람 대신 로봇으로 대체될 수 있을 것으로 예상된다. GTP라는 용어에서 파생되어 로봇이 로봇에게 피킹할 상품을 가져다주는 GTR(Goods-to-Robot)이라는 용어가 익숙해질 날이 머지않은 듯하다. 포장 작업 역시 많은 인력에 의존해 왔던 공정인데 세계적으로 다수의 기업이 고객의 주문량의 체적에 맞춘 재단형 무인화 포장장비를 상용화 출시하고 있다. 전후 공정/구간 이동용 AMR의 상용화 및 적용은 확산되고 있고 이외에도 Mixed 팔레타이징로봇, 상하차로봇 등도 활발한 PoC 및 실적용 사례가 나타나고 있는 등 물류센터 공정 운영 전체에 걸쳐 사람 대신 물류로봇으로 대체되는 무인 물류센터의 등장이 공상과학 속 이야기가 아닐 수도 있다.
글 | 두산로지스틱스솔루션 한종수 총괄위원 / 아주대학교 공학대학원 겸임교수